
Burnout and Castingīurnout is a procedure carried out to remove residual moisture and wax. Next, the wax inside the ceramic shell must be removed by putting the ceramic shell in an oven. The shell creates a hard exterior coating surrounding the pattern. The pattern is put in a ceramic slurry to build a shell. The wax pattern is then connected, forming a sprue and later a cluster. The process can be done several times depending on the parts that must be cast. Next, it is adjusted to make room for shrinkage. Producing the Wax PatternĪ wax pattern is formed from the semi-liquid wax poured into the die. Then, a die that is a negative relief to the part is created. The first step in the lost wax casting process is the formation of a three-dimensional rendering of what needs to be produced. The Lost Wax Casting Process Rendering the Wax Pattern Their use is found in chemical factories, aerospace, and marine environments. Nickel has great strength and resistance to heat, so nickel alloys are used in environments with extreme temperatures. For example, aluminum and manganese can be added to make it corrosion-resistant. The added elements of bronze enhance bronze's quality and performance. Yellow or red brass is used for lost wax casting for application and in door hardware and plumbing fixtures. Brassīrass's main defining properties are its polishing and finishing qualities. It is used to make parts for the automotive industry, aerospace, and military use. Cobalt is ideal for the process of lost wax casting because it is worn, corrosion, and heat resistant. Since cobalt is found combined within nature, the smelting process is used to separate it from alloys. Cobalt is not affected by oxidation due to a passivating film that covers it. CobaltĬobalt has a lustrous and hard finish that protects it and makes it resistant to oxidation. Aluminum alloys have a fluid nature that caters to parts with thin walls. When aluminum is alloyed and heat treated with other metals, it develops excellent strength, like that of low carbon steel. AluminumĪluminum is considered an ideal metal for lost wax casting because of its resistance to corrosion and machinability. After heat treatment, beryllium copper has excellent electrical and thermal conductivity. Beryllium Copperīeryllium copper makes castings that can be easily machined and have great ductility. Its main advantage is that it has multiple designs and is cost-effective. Ductile Ironĭuctile iron castings have excellent corrosion resistance, surface hardness, strength-to-weight ratio, and elasticity modulus. Its application can be found in the medical, aerospace, agricultural, and firearm sectors. Steel is used for lost wax casting because it is available in various grades, is economical, and can be heat treated to adjust its ductility.
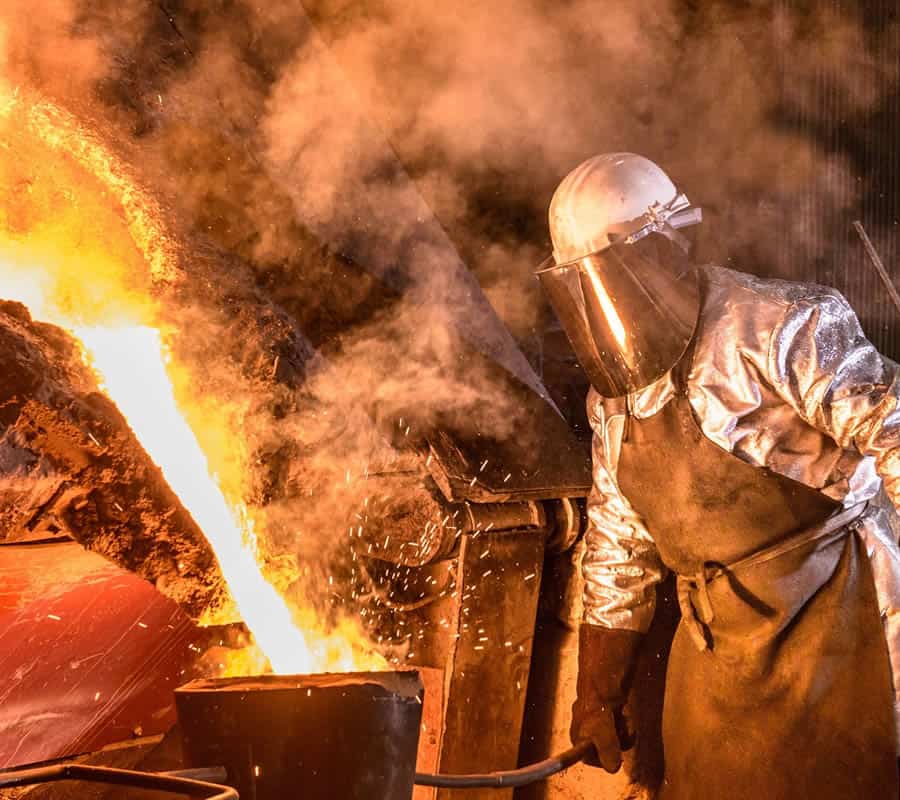

However, stainless steel has a percentage of chromium, making it resistant to oxidation and corrosive conditions. The combination of the alloys affects the endurance of heat and resistance to corrosion by the casting. Stainless steel consists of alloys such as nickel and chromium, which determine the mechanical and grain properties of the casting. Metals Used In Lost Wax Casting Stainless Steel
